How to Prepare a Model When Making a Polyurethane Rubber Mold
A model, also called a “master”, should be prepared according to the model material & mold material.
Models being used to make a polyurethane rubber mold often need to be prepared differently than models being used to make a silicone mold. Generally, silicone rubbers have better release properties than polyurethane rubber.
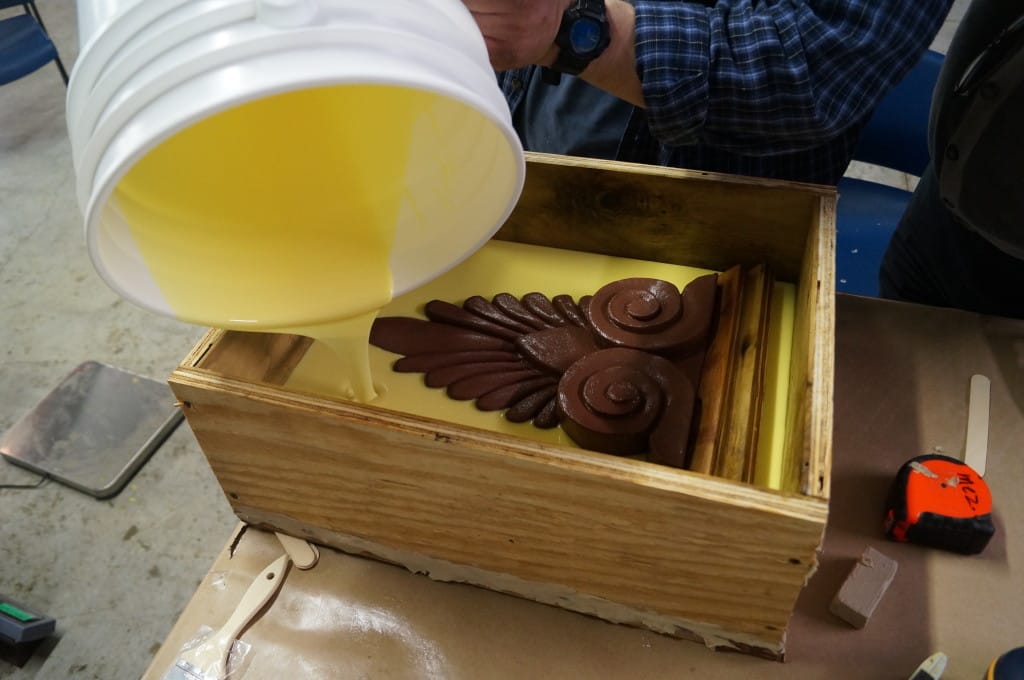
[Poly 74-20, a polyurethane rubber, being poured over a prepared clay model]
What Can Go Wrong
Incorrectly preparing a model for mold making can result in the rubber bonding to the model or the rubber not properly curing against the model.
Determine if the Model Requires a Sealing Agent
Porous models, such as wood, concrete, plaster, stone, pottery or masonry, must be sealed before applying any release agent or rubber.
[p.s. porous models should also be vented from beneath to prevent trapped air from forming bubbles in the rubber]
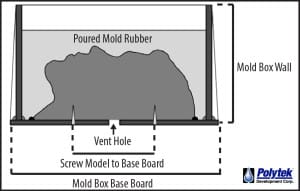
Sealing agents are designed to create a barrier so that liquid rubber does not penetrate pores in the model. Sealing pores reduces the chance that rubber can stick or mechanically lock on to the model. Generally, sealing agents are available in removable, semi-permanent, and permanent options.
Examples:
This very porous concrete stepping stone is sealed with two coats of a sealing agent before the mold making process:
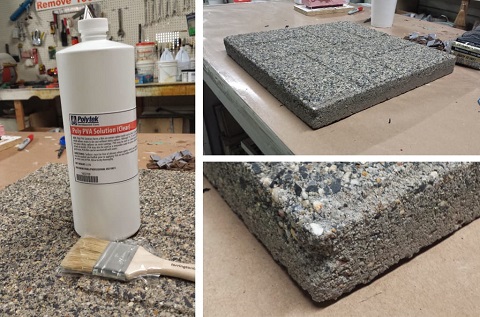
This non-porous plastic model does not require a sealing agent:
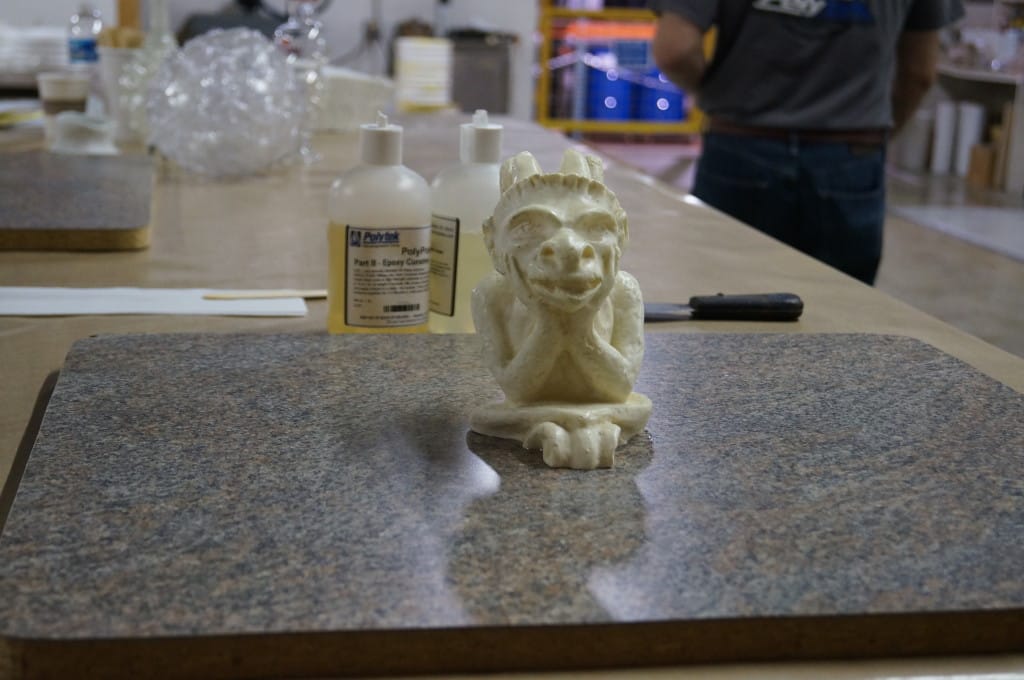
Other popular non-porous model materials include metals, wax, glazed ceramics, fiberglass, polyurethanes, and plasticine (even sulfur-containing clays do not generally require a sealing agent when working with liquid polyurethane mold rubbers).
Popular Sealing Agents for Porous Models
Some sealing agents can be purchased from your local home improvement or hardware store. Multiple coats of paste wax, dried and buffed, will seal most surfaces. Lacquer and paint are also used. For plaster, Potters soap works well (do not use soap on other model materials). The following sealing agents are available from Polytek (some of them serve as both a sealing agent and release agent):
Poly PVA Solution
This alcohol-based
sealer has one major advantage over many other sealing agents: it is water-soluble. This can be appealing for
those that would like to return the model to as close to original condition as possible
(NOTE: Even though Poly PVA can be removed, we cannot guarantee that the model will be in the
same condition it was at the start of the mold making process).
If this sealer is not washed off with water after the first mold is made, it should continue to act as a sealer if a second mold is made.
A release agent should be used in conjunction with this sealing agent; however, it should not be water-based. Release agent should not be applied until the PVA solution has dried, which takes approximately an hour after application (depending on temperature & humidity).
Poly PVA Solution is available in clear and green varieties.
Pol-Ease® 2350 Sealer & Release Agent
This semi-permanent sealer and release agent is white petrolatum dissolved in mineral spirits. It is considered semi-permanent because small amounts of the sealer can come off when the mold is cured and removed.
When applied correctly, additional release agent is not needed before making the polyurethane mold.
It is important to allow the solvent to evaporate before applying rubber; insufficient evaporation will cause cure issues in the polyurethane rubber.
PolyCoat Sealer & Release Agent
When this semi-permanent sealer & release agent is applied to a model, it leaves behind a thin silicone coating. Liquid polyurethane rubber can be applied directly to this coating without the use of additional release agent.
After applied, the solvent typically evaporates in ~5 minutes and the silicone cures in about 30 minutes (depending on temperature and humidity). Do not apply polyurethane rubber until it is completely cured.
Multiple molds can usually be made from one application of PolyCoat (multiple coats may be required if the model is very porous).
Apply a Release Agent
Release agents are coatings that are designed to prevent liquid rubber from sticking to surfaces.
Polyurethane rubbers naturally stick to a variety of materials; therefore, release agent should almost always be applied to the model before applying liquid polyurethane rubber.
Pol-Ease® 2300 Release Agentis the release agent that we most often recommend for this process. As a reminder, if Pol-Ease® 2350 Sealer & Release Agent or PolyCoat Sealer & Release Agent have been applied, there is no need to apply this additional release agent.
Liquid rubber can be poured over the model immediately after this release agent is applied – there is no wait time. In most cases, we recommend brushing out Pol-Ease 2300 with a dry brush after it is applied; this promotes even coverage. Applying too much release agent can cause pinhole surface defects in the mold.
Test Cures
If there is ever a question concerning compatibility between liquid polyurethane rubber and the prepared model surface, we recommend performing a small test cure on an identical surface to determine suitability.
Sealer & Release Agent Selection Guide
For an overview of all sealing and release agents available from Polytek (as well as a matrix that recommends which product to use for certain applications), view our Sealer & Release Agent: Selection Guide —
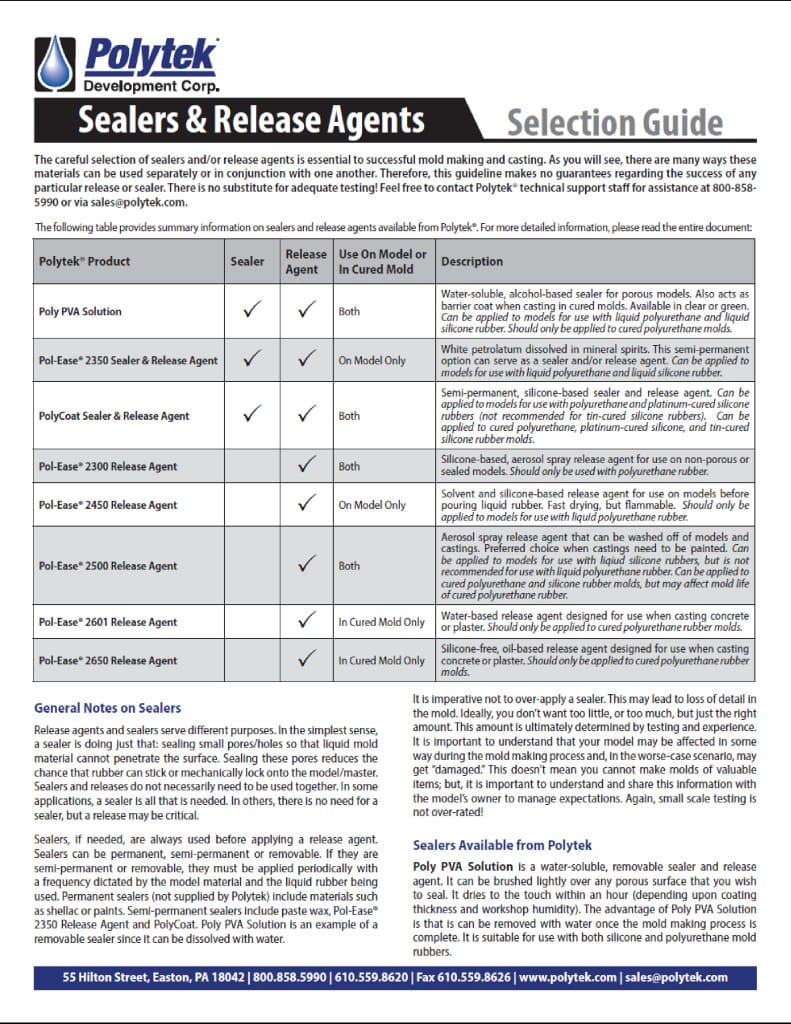